Porosity in Welding: Identifying Common Issues and Implementing Best Practices for Prevention
Porosity in welding is a prevalent issue that usually goes unnoticed till it causes considerable problems with the stability of welds. In this conversation, we will discover the essential aspects contributing to porosity formation, analyze its detrimental impacts on weld efficiency, and discuss the finest techniques that can be adopted to lessen porosity event in welding processes.
Typical Sources Of Porosity

An additional constant wrongdoer behind porosity is the visibility of impurities externally of the base steel, such as oil, oil, or corrosion. When these impurities are not effectively removed before welding, they can evaporate and come to be caught in the weld, triggering problems. Using unclean or damp filler products can introduce impurities right into the weld, adding to porosity problems. To reduce these common reasons for porosity, complete cleansing of base metals, proper securing gas choice, and adherence to optimal welding criteria are crucial methods in achieving top quality, porosity-free welds.
Effect of Porosity on Weld Quality

The existence of porosity in welding can dramatically compromise the structural stability and mechanical properties of welded joints. Porosity produces spaces within the weld steel, weakening its overall stamina and load-bearing ability.
Welds with high porosity degrees often tend to display lower impact strength and lowered capacity to warp plastically before fracturing. Porosity can impede the weld's capacity to properly send forces, leading to premature weld failing and possible security hazards in critical frameworks.
Finest Practices for Porosity Prevention
To boost the architectural stability and quality of welded joints, what details steps can be applied to lessen the event of porosity during the welding procedure? Utilizing the correct welding technique for the specific material being welded, such as changing the welding angle and weapon setting, can additionally protect against porosity. Normal inspection of welds and immediate remediation of any issues determined during the welding process are necessary methods to avoid porosity and generate high-grade welds.
Significance of Appropriate Welding Techniques
Implementing correct welding methods is extremely important in ensuring the architectural honesty and top quality of bonded joints, building on the foundation of effective porosity avoidance actions. Welding strategies straight affect the overall stamina and longevity of the bonded structure. One key aspect of correct welding methods is preserving the correct warmth input. Too much warm can lead to increased porosity as a news result of the entrapment of gases in the weld swimming pool. Alternatively, not enough warm might cause incomplete fusion, creating potential weak factors in the joint. Furthermore, using the proper welding specifications, such as voltage, existing, and take a trip rate, is vital for accomplishing sound welds with minimal porosity.
Additionally, the selection of welding process, whether it be MIG, TIG, or stick welding, must align with the particular needs of the project to make sure optimum results. Proper cleansing and preparation of the base steel, in addition to picking the right filler material, are additionally essential elements of skillful welding techniques. By adhering to these finest techniques, welders can minimize the threat of porosity formation and generate top quality, structurally sound welds.
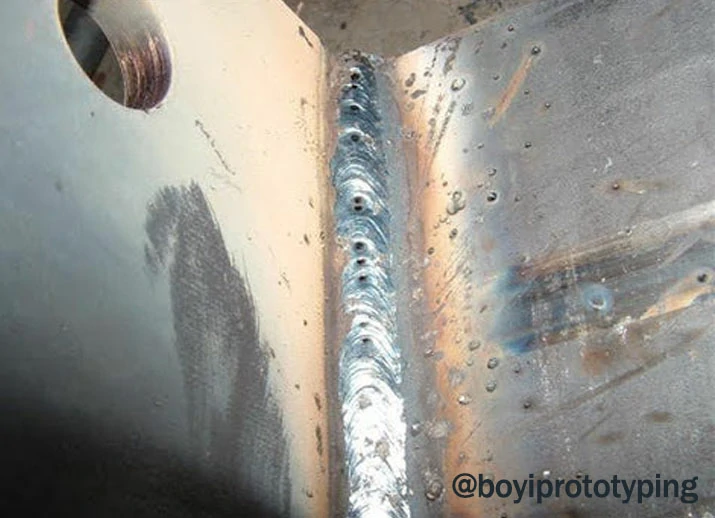
Examining and Quality Control Procedures
Testing treatments are essential to detect and prevent porosity in welding, ensuring the strength and resilience of the final product. Non-destructive screening approaches such as ultrasonic screening, radiographic testing, and visual inspection are commonly used to recognize prospective problems like porosity.
Post-weld examinations, on the other hand, evaluate the last weld for any problems, consisting of porosity, and confirm that it satisfies defined criteria. Implementing a detailed top quality control plan that includes complete testing procedures and evaluations is extremely important to reducing porosity issues and making sure the total top quality of welded joints.
Conclusion
In final thought, porosity in welding can be a typical concern that influences the top quality of welds. By identifying the common reasons for porosity and executing ideal practices for avoidance, such as proper welding techniques and testing measures, welders can guarantee excellent pop over to this site quality and trustworthy welds. It is important to focus on prevention methods to minimize the incident of official source porosity and preserve the honesty of welded frameworks.